Excitement About Alcast Company
Table of ContentsA Biased View of Alcast CompanyThe Basic Principles Of Alcast Company Alcast Company for BeginnersSome Known Details About Alcast Company The Buzz on Alcast CompanyExcitement About Alcast Company
Chemical Contrast of Cast Light weight aluminum Alloys Silicon advertises castability by minimizing the alloy's melting temperature level and improving fluidness during casting. In addition, silicon contributes to the alloy's stamina and wear resistance, making it valuable in applications where longevity is essential, such as vehicle components and engine elements.It additionally improves the machinability of the alloy, making it much easier to process right into ended up products. This way, iron adds to the overall workability of light weight aluminum alloys. Copper boosts electric conductivity, making it beneficial in electrical applications. It likewise enhances corrosion resistance and contributes to the alloy's total strength.
Manganese adds to the strength of light weight aluminum alloys and boosts workability (aluminum foundry). It is commonly used in wrought aluminum items like sheets, extrusions, and accounts. The presence of manganese aids in the alloy's formability and resistance to breaking during fabrication processes. Magnesium is a lightweight element that offers stamina and effect resistance to aluminum alloys.
The Main Principles Of Alcast Company
It allows the production of light-weight components with superb mechanical properties. Zinc enhances the castability of light weight aluminum alloys and assists manage the solidification procedure during casting. It enhances the alloy's stamina and solidity. It is often found in applications where elaborate forms and fine information are essential, such as decorative spreadings and particular vehicle parts.
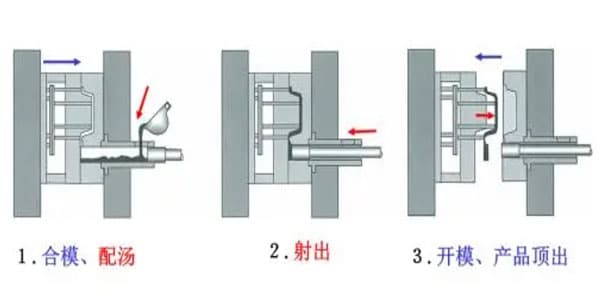
The primary thermal conductivity, tensile stamina, return strength, and elongation differ. Among the above alloys, A356 has the highest thermal conductivity, and A380 and ADC12 have the cheapest.
Indicators on Alcast Company You Should Know
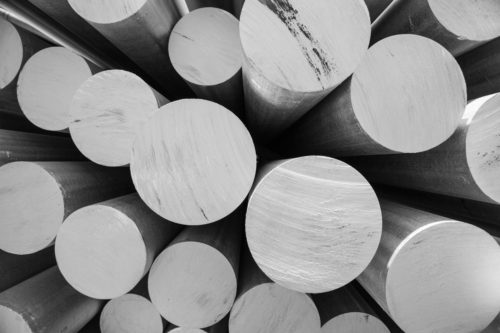
Its special buildings make A360 an important selection for accuracy spreading in these sectors, enhancing item toughness and high quality. aluminum foundry. Aluminum alloy 380, or A380, is a widely utilized spreading alloy with numerous distinctive qualities.
In precision casting, aluminum 413 beams in the Customer Electronic Devices and Power Equipment sectors. This alloy's remarkable deterioration resistance makes it an outstanding choice for outside applications, ensuring durable, resilient products in the pointed out industries.
Alcast Company Things To Know Before You Buy
The light weight aluminum alloy you pick will considerably influence both the casting procedure and the residential or commercial properties of the final item. Due to the fact that of this, you must make your choice thoroughly and take an informed technique.
Establishing one of the most appropriate light weight aluminum alloy for your application will mean evaluating a wide array of attributes. These comparative alloy attributes comply with the North American Pass Away Spreading Association's guidelines, and we have actually split them into two groups. The why not try these out initial category addresses alloy qualities that influence the manufacturing procedure. The second covers characteristics influencing the properties of the last item.
What Does Alcast Company Mean?
The alloy you choose for die spreading straight affects a number of aspects of the spreading process, like just how easy the alloy is to collaborate with and if it is prone to casting defects. Hot breaking, additionally referred to as solidification fracturing, is a regular die casting problem for aluminum alloys that can result in internal or surface-level rips or splits.
Certain aluminum alloys are more susceptible to warm splitting than others, and your choice must consider this. It can harm both the cast and the die, so you need to look for alloys with high anti-soldering residential properties.
Corrosion resistance, which is already a significant feature of light weight aluminum, can vary considerably from alloy to alloy and is an essential particular to consider depending upon the ecological problems your item will certainly be subjected to (Aluminum Casting). Use resistance is an additional building commonly looked for in light weight aluminum items and can separate some alloys